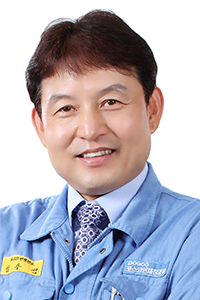
우리는 살면서 그냥 보이는 것으로 쉽게 사물을 판단하고 보이지 않는 것의 중요성을 생각하지 않는 경우가 많다. 사람을 처음 만날 때도 그 사람의 옷차림이나 인상, 태도 등 보이는 모습만으로 본인의 경험에 비추어 판단하는 경향이 크며, 그 사람의 성장과정이나 인성 등 내면적인 면을 생각하고 파악하는 것에 소홀해질 수 있다. 우리가 눈(目)을 표현할 때 육안도 있지만 보이지 않는 것을 보는 눈인 심안, 혜안, 천안 등의 단어도 많다는 것을 간과해서는 안된다.
기업(企業)이라는 한자의 어원적인 의미는 ‘사람(人)이 일(業)로 머무른다(止)’는 뜻이다. 기업에 일하는 사람이 머무르기 위해서는 보이는 부분인 이익창출이 이어져 일하는 사람에게 그에 합당한 보수를 지불하고 경제적인 문제도 해결돼야 하지만, 보이지 않는 부분인 일을 통해 개인의 성장과 발전도 함께 이뤄져야 한다는 의미도 상당히 중요하다고 본다. 이 두가지를 동시에 해결할 수 있는 방법이 현장의 낭비를 발굴하고 제거하는 개선활동인 것이다. 낭비를 발굴하고 개선하는 직원의 능력이 보이지 않는 부분이며, 이를 통해 원가가 절감되어 이익이 창출되는 부분은 가시적인 성과라 할 수 있다.
생산현장에는 고객이 주문하는 품종과 수량이 수시로 변동되므로 재료, 설비, 사람이 투입되고 대응하는 제조과정에서 불필요, 불균일, 불합리 등의 낭비요인이 따르게 된다. 이를테면 과잉생산·재고·운반·가공·동작·불량·대기 등에서 오는 낭비가 손실을 초래하고 원가를 잡아먹는 ‘7대 낭비’로 일컬어진다. 이 중 가장 나쁜 낭비는 ‘과잉생산’이며 고객이나 후공정이 필요로 하지 않는 시간에 제품을 미리 만들어 놓는 것을 말한다. 이로 인해 창고나 저장공간이 필요하게 되며 재고가 쌓이고 대기시간도 길어지게 된다. 또한 저장공간이 부족해져 또 다시 이동과 동작이 발생하며 재취급하는 과정에서 잘못하여 많은 사람이 공들여 만들어 놓은 제품이 재차 불량이 되는 낭비의 악순환이 되기도 한다. 물론 과잉생산을 포함하여 생산과정에서 유발되는 각각의 낭비는 별개적으로 수시 발생하기도 한다.
필자가 수년 전 컨설팅한 내화물 생산공장에서는 과잉생산의 낭비를 줄이기 위한 노력을 집중했었다. 즉, 7개의 품목을 1주일간 1일씩 생산하여 창고에 대량으로 저장하여 출하량에 대응하던 공정을 제품별 준비교체 전담반을 신설하여 획기적으로 품명교체 시간을 줄이고, 일별 출하량에 맞춰 하루에 3~4품목씩 2일 패턴으로 주 3회 생산하도록 종류와 수량을 평준화하여 공정 내 저장공간과 재고를 50% 이상 현저하게 절감하여 낭비를 줄인 사례가 있다.
이렇듯 현장의 보이지 않는 낭비를 구분하여 보이도록 하고 지속적으로 공정의 레이아웃과 생산능력을 개선해 나간다면, 불필요한 생산으로 인한 과잉생산의 낭비와 재공, 재고의 낭비가 대폭 줄어 전반적으로 회사의 이윤창출이 가능해진다. 거기에 직원들의 낭비 발굴과 개선하는 역량까지 향상돼 공간적으로는 일하는 직원과 회사가 좋아지고, 시간적으로는 지속발전가능한 영속기업이 될 것이다.